What is a load cell?
A load cell is a sensor or a transducer that converts a load or force acting on it into an electronic signal. This electronic signal can be a voltage change, current change or frequency change depending on the type of load cell and circuitry used.
Load cells or Load sensors as they are commonly called – can be made using resistive, capacitive, inductive or other techniques. Most commonly available load cells are based on the principle of change of resistance in response to an applied load. This is termed piezo-resistive i.e. something that changes in response to an applied pressure (or squeezed). Loadstar Sensors has pioneered the use of capacitive techniques to build rugged, small digital load cells with high level USB, WiFi, XBee Wireless and Bluetooth outputs. We have over a dozen patents covering various aspects of capacitive and digital load cells. We have also developed a variety of convenient low cost easy to use, digital and analog interfaces that enable incorporation of load cells and other sensors into a variety of applications.
Commonly available load cells include:
– S-Beam Load Cell
– Single Point Load Cells
– Shear Beam Load Cells
– Pancake Load Cells
– Button Load Cells
– Through hole Load cells and
– Miniature and Sub-Miniature load cells
Load Cells – How They Work?
Load cells are traditionally built using resistive bonded foil strain gauges (as shown in the picture below). Strain gauges are essentially resistors built using standard semiconductor etching techniques and are bonded to a metallic member such as a cantilever beam or diaphragm.
Usually at least four strain gauges are configured in a Wheatstone Bridge configuration with four separate resistors connected as shown below in what is called a Wheatstone Bridge Network. An excitation voltage – usually 10V is applied to one set of corners and the voltage difference is measured between the other two corners. At equilibrium with no applied load, the voltage output is zero or very close to zero when the four resistors are closely matched in value. That is why it is referred to as a balanced bridge circuit.
When the metallic member to which the strain gauges are attached, is stressed by the application of a force, the resulting strain – leads to a change in resistance in one (or more) of the resistors. This change in resistance results in a change in output voltage. This small change in output voltage can be measured and digitized after careful amplification of the small milli-volt level signals to a higher amplitude 0-5V or 0-10V signal.
These load cells have been ins use for many decades now, and can provide very accurate readings but require many tedious steps during the manufacturing process.
The steps involved in manufacturing strain gauge based load cells include:
- Machining of an intricate pattern to optimize stress & strain on the mechanical member
- Controlling surface roughness through surface polishing to ensure rough edges are removed prior to bonding a strain gauge
- Scoring to make alignment marks to align multiple strain gauges that need to be bonded to create the Wheatstone bridge
- Application of a bonding agent with matching temperature coefficients to the metal being used
- Applying even pressure on the strain gauge during the curing process to avoid lumpiness along the bond
- Curing at an elevated temperature in an oven to cure the bonding agent and temper the bond
- Applying a coating to protect the strain gauges and wiring from moisture and humidity and environmental effects
Once the load cells are built, they need to be tested at different temperatures in order to ascertain their drift with temperature. Thermistors are installed to reduce the temperature effect at zero loads and then at full scale loads prior to final test and calibration.
As you can see – the resistive load cells are cumbersome to build and require many manual steps during their manufacture.
However, when built properly from a trusted source, resistive load cells built with bonded foil strain gauges, offer accuracies as good as +/- 0.02% of full scale! And when properly compensated for temperature variations they can be used between -10C to 40C generally with very good resistance to temperature variations. Finally, these load cells offer excellent off-center load compensation and hence are very useful for building scales where the weight to be measured could be placed randomly anywhere on the loading platform.
What are Capacitive Load Cells? How do they work?
Capacitive load cells are built on the principal of a change in capacitance when a force is applied on the load cell. Capacitance is the ability of a system to store a charge. If a capacitor is built using the classic parallel plate approach then its ability to store a charge is directly proportional to the area between the two plates and inversely proportional to the gap between the plates.
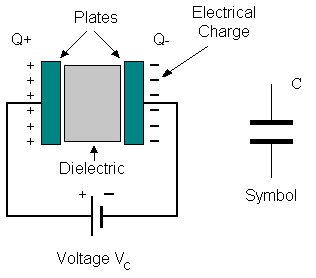
The construction of a capacitive sensor is much simpler than constructing a resistive load cell. In addition, by optimizing the starting gaps and/or overlap areas of the two plates, once can vary the sensitivity and output signal to optimize it for various applications.
Capacitive techniques can be used to measure gaps (proximity), humidity, tilt, force, torque, acceleration, fluid quality and many other physical parameters! It is a very versatile parameter that offers tremendous sensitivities in a small package.
This capacitive technology is more rugged than strain gauge designs and can therefore be used in a wider variety of engineering applications. When coupled with USB wireless technology, these load sensors can be used for easy measurement on a PC and for data sharing on the Internet.
Load Sensors Available in Digital and Analog Designs
The iLoad Series Load cells built on capacitance technology come built in with both analog- and digital outputs! Using a simple hybrid adapter, one can simultaneously read the digital output on a PC while measuring the analog output on a voltmeter or data acquisition system!
This unique hybrid output feature enables developers to monitor the sensor output on a PC while debugging their embedded application which samples the analog output.
These units have a variety of features, including:
- Digital and Analog (0-5V DC) output
- Wired (Analog or Digital USB) and Wireless outputs (XBee Wireless, WiFi or Bluetooth)
- Rugged construction
- Small sizes
- High data output rates (> 500 Hz)
- Versatile shapes and patterns
- Sensitive readings for increased accuracy
- Reduced environmental effects
Load sensors are available in a variety of sizes and capacities from 2 lbs to 10,000 lbs to suit different engineering applications. Some models are only about a half inch diameter and only 0.1 inches high, so they can fit into tight locations such as when used in a medical device application. While the standard circular shape works for most applications, custom fittings are also available.
Loadstar Sensors, Inc. makes capacitive load cells with both analog and digital outputs. We also sell a variety of PC friendly networking accessories and indicators in addition to our weight based measurement and control software.
Load Cell Selection Guidelines
When you measure forces or loads, in addition to the capacity and size of the load cell, a number of application requirements need to be carefully considered. These include:
- Operating Temperature Conditions (Well controlled, room temperature or outdoor, harsh environments with changing humidity and temperature)
- Duration of measurement (Short term measurement with a Tare or longer term measurements where Tare is not feasible)
- Absolute Accuracy Required (as a percentage of full scale output or as a percentage of reading)
- Direction of loading (tension or compression or both)
- Certifications Needed (for trade applications needing NTEP or OIML certifications or test and measurement needing ASTM E-74 OR R & D)
- Mounting Options (Fasten sensor on both sides or no need for fastening at all)
- Output required (Analog mV/V, 0-5V, 4-20mA, Digital USB, Digital Wireless, Digital RS-232/485)
- Measurement Speed (1Hz or up to 100Hz or faster than 100Hz)
- Total cost of operation (small quantity or large volumes)
In general, our capacitive load cells are an excellent integrated solution for measuring forces/loads for R & D environments. They offer high sensitivities in a very rugged package with easy mounting options to incorporate into your application. Our sensors offer direct connectivity to PCs and make it effortless to write software applications. These are suitable for a wide variety of general purpose applications where accuracies required are in the range of +/- 0.25% to +/- 1% of full scale loads and will be used at steady state room temperature conditions around 25C such as what is found in temperature controlled labs, schools, R&D facilities etc.
When you need very high accuracies, NTEP/OIML Certifications and need long term stability, for those applications we recommend you use our resistive load cells with either the DI-1000 Series Digital Load Cell Interfaces or the AI-1000 Series Analog Interfaces for your application. If you are still unsure about which type of load cell you may need feel free to contact us.